The Future of 3D printing in the Automotive Industry
The automotive industry has been the driving force for 3D printing ever since its formation: so much so that the technology researcher SmarTech predicts that 3D printing in the automotive industry will be worth $1.1 billion a year by 2019.
3D printing is at the core of the car industry, and we’re close to having fully printed cars from the ground up. Its uses have even expanded to the movie industry – the Aston Martin that was riddled with bullets in the 2012 James Bond movie, Skyfall, was something you needn’t have cringed about: the model used for production was a 3D printed version.
So, how has 3D printing changed the face of the automotive industry already?
Koenigsegg’s One: 1
Hypercar manufacturer Koenigsegg has always been ahead of the curve in its innovative and advanced methods of production. The turbo on its new model, the ‘One: 1’, was only made possible with 3D printing in order to bring Christian von Koenigsegg’s vision to life.
3D printing allowed a narrow inner turbo housing, and a larger unit, in one that allowed him to get the best possible acceleration and high end performance. These are conflicting demands, and 3D printing gave the company a solution to a conundrum that has vexed the likes of BMW and Mercedes.
Local Motors: The Strati
Local Motors, the creators of the fully 3D-printed car the Strati, believe that in the future, 3D printing will be the main way in which cars are manufactured. The Strati was composed of a mere 47 parts instead of the 35,000 typical for a standard car, and can be assembled within 44 hours.
If the Local Motors dream comes true, the world will become populated by so-called micro-factories, all printing cars that are not only crowd funded but also crowd designed. The car’s creation is ‘like Lego,’ as described by the company’s chief marketing officer, Elle Shelley, and though somewhat less easy on the eyes than the Koenigsegg, still looks set to shake up the automotive industry.
Williams, F1 Engineering
Formula One is undoubtedly the most technically advanced sport on the planet; cars are developed constantly throughout the year by teams with their finger on the technological pulse. With its culture of cutting edge tech, and the help of wind-tunnel development and testing results, the team can often change the car radically between races that are two weeks apart.
British team Williams Martini Racing has developed a method of 3D printing small parts in Alumide and CarbonMide, including full gearbox assemblies for functional testing and production aero parts. This puts the company streets ahead of its competitors, and should see the benefits of its innovation appear on the podium very soon.
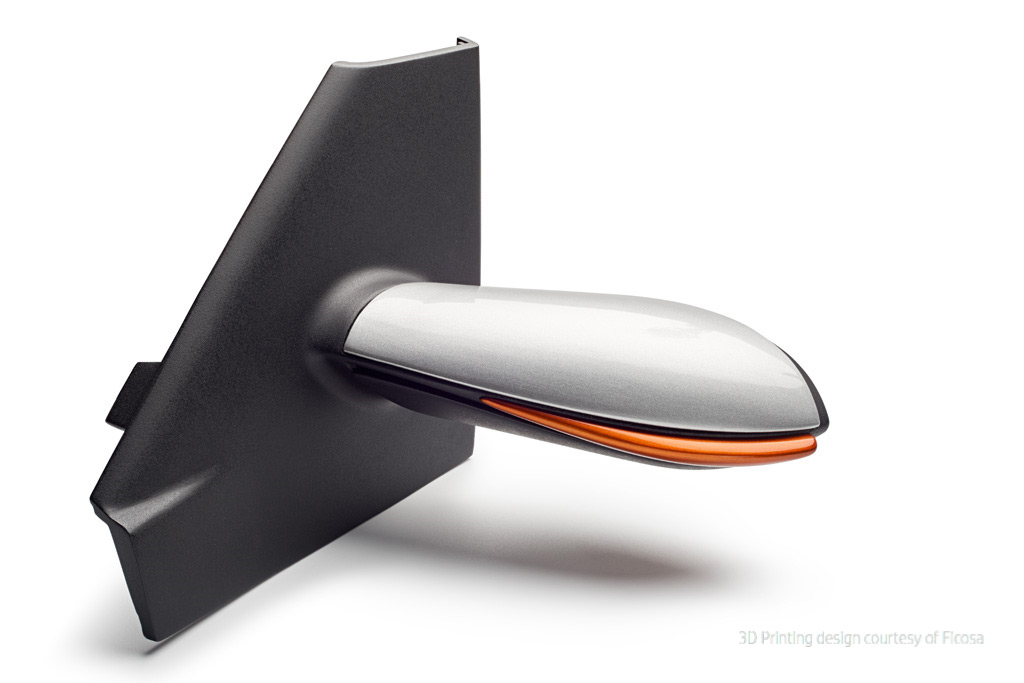
HP Jet Fusion 3D Print of wing mirror courtesy of Ficosa
The Future
So it’s clear that 3D printing is the way forward when it comes to automotive engineering. Until now the adoption of 3d printing has been limited to either prototyping or low volume production, however the introduction of technologies such as HP’s jet fusion 3D printing technology looks set to change how automotive companies approach rapid manufacturing. Lower materials costs, and build speeds up to 10 times faster than traditional SLS technology means 3d printing is now truly an option for the production of functional parts on a car. SmarTech reports:
‘Use of 3D printing in automotive is evolving from relatively simple concept models for fit and finish checks and design verification, to functional parts that are used in test vehicles, engines, and platforms. This represents a shift in 3D printing adoption towards higher value applications and is an early step towards acceptance of 3D printed end-use parts in automobiles.’
The forward-thinking industry has found its niche in the revolutionary methods of manufacturing parts for its engines, gearboxes and – in the case of the little Strati – the entirety of the car itself. We might be driving a fully printable vehicle sooner than we think…